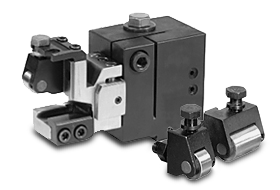
Shaving Tools
Slater Tools offers Shaving Tool Holders, Shaving Tool Blanks, Shaving Roll Rests and other accessories for various types of machines. Shaving will produce round diameters on size within +/- .0005. With these shaving tools, contours can be produced that would otherwise only be possible by tracing. By its nature, shaving can almost always be completed in fewer revolutions than an end-working operation. Shaving also has its built-in diameter controls; it does not rely on exact cross slide stroke length for accuracy, and to a certain extent, it can compensate for index or spindle errors.